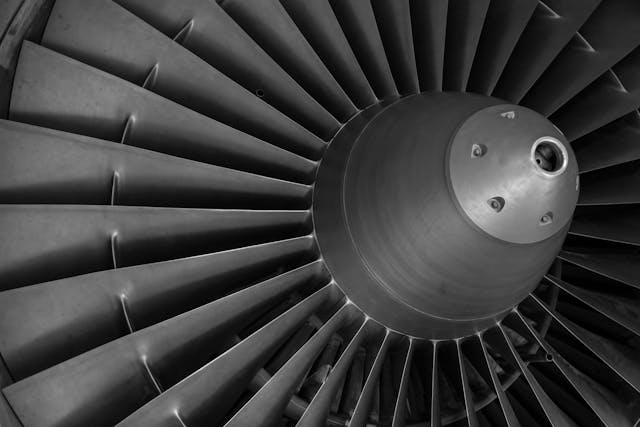
DIFFERENT METHODS OF TURBINE COOLING
In the energy engineering sector, turbine cooling is crucial for ensuring efficiency and longevity. Different cooling methods help maintain stable internal temperatures, reducing wear and extending the turbine’s operational life. In this article, we explore the main turbine cooling methods and the associated maintenance requirements.
1. Air Cooling
Air cooling is one of the most common methods. This system uses compressed airflow to reduce internal temperatures, preserving the turbine’s structural integrity. A key challenge is the need for regular maintenance to prevent debris buildup and efficiency losses. It’s essential to inspect and clean the ventilation paths regularly to ensure smooth airflow.
Advantages:
- Simpler structure
- Lower implementation costs
Disadvantages:
- Limited efficiency in extreme conditions
- Increased need for airway cleaning
2. Liquid Cooling
Liquid cooling uses special fluids to dissipate heat. This method is more efficient but requires additional components like pumps and pipes, which can increase maintenance complexity. During maintenance, it’s important to check for leaks or blockages and periodically replace fluids to avoid corrosion.
Advantages:
- Effective even at high temperatures
- Greater thermal stability
Disadvantages:
- High implementation costs
- More complex maintenance
3. Hybrid Cooling
Hybrid cooling combines air and liquid cooling elements, offering a balanced solution for complex turbines. This combination allows for cooling method adaptation to different operating conditions, improving efficiency and reducing maintenance frequency. However, it’s essential to monitor both systems constantly to ensure harmonious operation.
Advantages:
- High efficiency in various operating conditions
- Increased flexibility
Disadvantages:
- Requires constant monitoring
- Higher implementation and maintenance costs
Maintenance Requirements
For each cooling system type, maintenance is critical. Establishing a regular maintenance plan is essential to avoid technical issues and optimize turbine longevity. Thermal monitoring, component cleaning, and leak checks are indispensable practices to ensure operational continuity.